摘要:化學(xué)機械拋光(CMP)技術(shù)是目前廣泛采用的幾乎唯一的高精度全局平面化技術(shù)。拋光后表面的清洗質(zhì)量直接關(guān)系到CMP技術(shù)水平的高低。介紹了各種機械、物理及化學(xué)清洗方法與工藝技術(shù)優(yōu)缺點,指出了清洗荊、清洗方式是CMP后清洗技術(shù)中的關(guān)捷要素。綜述了CMP后清洗技術(shù)的發(fā)展現(xiàn)狀,分析了CMP后清洗存在的問題,并對其發(fā)展趨勢進行了展望。
關(guān)鍵詞:化學(xué)機械拋光;原子級精度表面;清洗技術(shù)
0引言目前因拋光后表面清洗不干凈引起的電子器件產(chǎn)品合格率降低,占次品率的50%左右,清洗質(zhì)量的高低已嚴(yán)重影響到先進電子產(chǎn)品的性能、可靠性與穩(wěn)定性。工藝中si片表面吸附的微粒、有機和無機粘污會破壞極薄氧化層的完整性,導(dǎo)致微結(jié)構(gòu)缺陷,引起低擊穿、管道擊穿、軟擊穿、漏電流增加以及芯片短路等問題?1。計算機硬盤技術(shù)中,隨著硬盤存儲密度的快速上升,磁頭的飛行高度已降低到10姍以下L2J。原子級表面粗糙度(原子直徑小于0.3nm)、無微觀缺陷、潔凈的高精表面已成為高技術(shù)電子產(chǎn)品制造中的共同要求,也是關(guān)系其性能的關(guān)鍵因素。
目前一般采用CMP技術(shù)進行片子表面的高精度全局平坦化。由于拋光后新鮮表面活性高,以及CMP拋光液中大量使用高濃度的納米磨粒(如納米Si02、納米AIO粒子)、多種化學(xué)品等因素,工件表面極易吸附納米顆粒等污染物,導(dǎo)致CMP后清洗極其困難。集成電路技術(shù)中,對0.35pm及以下的CMOS工藝,要求后清洗提供的片子上0.12弘m以上附著物不多于500個/m2,各種金屬雜質(zhì)如Fe、cu、cr等控制在目前分子分析技術(shù)的檢測極限以下(約為1010原子/cm2)等【3】。下一代計算機垂直存儲技術(shù)對硬盤基片表面潔凈度的具體要求為:表面殘留顆粒(大于200nm)不超過15個/片,表面殘留陰離子和陽離子分別不超過1∥片,殘留有機物(硅油、胺)小于1ng/cm2。并且清洗后不能造成新的損傷與污染物殘留。CMP后超光滑表面的超精密清洗技術(shù)已成為超精密加工技術(shù)中急待解決的關(guān)鍵性難題之一。1CMP后清洗技術(shù)及研究現(xiàn)狀
清洗是利用物理、化學(xué)或機械作用的方法使吸附在表面的污染物解吸而離開物體表面的過程。物理方法是利用光、電、熱等物理作用使污染物獲得能量,通過自身的振動而脫離基體表面;化學(xué)方法則是利用清洗劑和扮染物進行化學(xué)作用,使大分子污染物生成可溶于清洗劑的小分子物質(zhì)而脫離基體表面或破壞污染物與基體表面之間的鍵合作用而使之脫離;機械方法是利用摩擦等機械能作用,使表面吸附的顆粒等污染物脫離表面。
在超光滑表面的清洗中,不同工件、不同工序?qū)Ρ砻媲鍧嵍鹊囊蟛煌?,必須針對不同的對象及目的采取不同的清洗方法,以滿足工藝對清潔度的要求【4]。目前超光滑表面清洗技術(shù)總體上可分為濕法和干法清洗。濕法清洗一直是晶片清洗技術(shù)的主流。它是利用溶劑、各種酸堿、表面活性劑和水的混合物通過腐蝕、溶解等化學(xué)反應(yīng),結(jié)合一定的機械作用以去除晶片表面的沾污物。
1.1清洗方法與工藝技術(shù)目前常用的CMP后清洗的方法有浸泡、噴淋、擦洗、超聲波、兆聲波[5]等。其中浸泡、噴淋大多作為中間過程,不是單獨的清洗方法。
擦洗是一種應(yīng)用廣泛、低廉、高效的接觸式清洗方式,是刷子和工件表面持續(xù)接觸的介于邊界到彈流潤滑的摩擦學(xué)過程,通過刷子與Si片表面的接觸力結(jié)合液力的拖曳力作用,去除Si片表面拋光過程中滲入的顆?!荆?/span>
J。J.M.Lim等人【7]發(fā)現(xiàn)擦洗可有效清除Si片表面上直徑大于0.2坤I{陵子污染物,但對清除金屬離子、有機物沾污效果不佳。N.Mmm圮n、A.PhiUipossian等人[8-93通過調(diào)節(jié)刷子壓力、轉(zhuǎn)速、清洗液pH值等參數(shù)影響擦洗的摩擦學(xué)狀態(tài),從而影響清洗過程及沾污顆粒的去除效果。G.她等人[10]給出擦洗過程中,固體表面上亞微米粒子受清洗流體的Stokes拖曳力(FD)的公式為
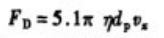
式中:可是流體黏度;d。是粒子直徑;%是在粒子中心與基片平行的流體速度??梢娏W釉酱?,液體拖曳力越大,越容易被去除。
擦洗方法易產(chǎn)生表面損傷。液體動力邊界層的提升力較小,不足以移除si片表面拋光過程中滲入的顆粒,必須依靠擦洗刷子與Si片表面的直接接觸力結(jié)合液力的拖曳作用力才能使之有效去除【6]。但因接觸壓力的存在,刷子脫落物會引起新的污染,并且刷子壓力會造成新的表面損傷[11J。如A.A.Busnaina等人[12J指出顆粒/刷子接觸對于清洗的影響,當(dāng)刷子與粒子相距1pm時,很難清除0.1gtmD.X下的粒子,全接觸可清除納米級粒子,但可能會引起表面損傷。H.Liang等人【13J也發(fā)現(xiàn)擦洗過程中刷子與工件表面間存在滑動磨損,會造成新的表面損傷。
作為非接觸式表面清洗,超聲波以其清洗方便、效率高等優(yōu)點得到廣泛應(yīng)用。超聲波清洗的頻率一般在20—40kHz。其機理主要是利用空化效應(yīng)而產(chǎn)生高達數(shù)千大氣壓的沖擊壓力和局部高溫以及超聲波對媒液的攪拌作用使附著的污染物脫離表面。
超聲波清洗控制參數(shù)包括超聲波頻率、清洗溫度和清洗時間等。超聲波清洗中,對粒子施加的能量(iv)可描述為
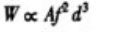
式中:.廠為頻率,d為粒子直徑??梢娏W釉酱?,得到的能量越大,越易脫離。故超聲波主要用來清除表面吸附的較大的粒子污染雜質(zhì)(如1pm以上)。隨著粒子尺寸的減小,其清洗效果下降,對于O.2ttml)2上下的納米級污染物,就難以去除,而且該頻率下產(chǎn)生的駐波易對片子造成損傷。
近來,針對超聲波清洗的局限性,兆聲波清洗得到一定重視。兆聲波清洗的機理是采用高頻(O.8。1.0Mnz)交流電激勵壓電陶瓷晶體,使它產(chǎn)生振動。振動產(chǎn)生兆聲波,使si片表面附近產(chǎn)生薄的聲學(xué)邊界層,溶液中產(chǎn)生的壓力振動以及超高頻的高能量,從而產(chǎn)生極大的聲壓梯度、粒子速度以及聲流作用等,使Si片表面吸附的污染物及微粒被強制除去并進入清洗溶液中。清洗溶液處在不停地從底往上流動和過濾循環(huán)中。由于頻率過高,空化作用在清洗中不起主要作用,與超聲波清洗相比,超聲波清洗難以清除小于1ttm的微粒相比,兆聲波清洗對表面損傷較小,可除去0.2胂以下的粒子。清洗溫度、清洗時間、兆聲波功率等參數(shù)均可影響顆粒的去除效果【l制。A.A.Busnaina等人[15]通過優(yōu)化清洗溫度、清洗時間、兆聲波功率等參數(shù),對于si片表面吸附的納米級si02粒子能達到99%以上的清洗效率。
隨著對表面潔凈度要求的提高,為有效去除si片表面CMP后的微米及納米級微粒,激光誘導(dǎo)振蕩、等離子體、氣相、臭氧.紫外、干冰等新型清洗技術(shù)[16-17]也得到探索與研究。等離子體清洗利用高速運動的離子束轟擊被清洗物表面,將動能傳遞給污染物粒子。這種方法常通過氧等離子體去除有機沾污,并加速其與等離子體中的活性基反應(yīng),使之解吸,但其效率較低、成本較高。激光誘導(dǎo)振蕩清洗可有效去除Si片表面CMP后的微米及納米級微粒,清洗效率強烈依賴于激光焦點與si片表面間距離及該距離的控制。目前這些方法大多處于科研階段,未達到實用化的程度。鑒于各種清洗方法的優(yōu)缺點,可以預(yù)料幾種具有互補作用的清洗方法組合使用,實現(xiàn)“高效率、高質(zhì)量、低損傷”清洗將是清洗方法與工藝的發(fā)展趨勢。
1.2清洗劑
清洗過程中,清洗劑的組成和組分對于清洗質(zhì)量與效率起關(guān)鍵作用。標(biāo)準(zhǔn)RCA法[加,1s】是集成電路工藝中至今仍廣泛使用的清洗方法。傳統(tǒng)的.RCA法交替使用雙氧水+氨水(SC.1溶液)、雙氧水+鹽酸(SC.2溶液)兩種清洗劑,可有效除去金屬離子及有機污染物。其他廣泛報道的用于集成電路的清洗液有采用稀HF及?。龋疲埃秤糜冢螅槠茫停泻笄逑础ⅲ悖?、隔層電介質(zhì)膜的CMP后清洗,降低si片表面氧化硅顆粒和金屬粘污量【l列;含2%氟硼酸的40%磷酸溶液去除鑲嵌w的SiCMP后表面顆粒L201;四甲基氫氧化銨(TMAH)用于wCMP后清洗【2等。
用于高精表面的清洗劑成分和配方往往是作為有關(guān)企業(yè)的核心技術(shù)予以重點保護的。如專利TW499478.A報道了含有多羥基化合物的水基清洗液;US2003077983一A1介紹了一種酸基蝕刻劑,用以去除硬盤或磁頭基片表面吸附的拋光液顆粒;W02003002688.A介紹了一種無氟清洗液,由二羧基酸、羥基羧酸及其鹽或二者混合物的水溶液構(gòu)成,用于去除集成電路基片表面的吸附顆粒;TW422745.A介紹一種基片的清洗方法,使用堿溶液、氫氧化銨、過氧化氫溶液去除拋光液顆粒,使用氫氟酸去除介電層顆粒,使用鹽酸和過氧化氫溶液去除滲入到基片表面的金屬離子;W0200124242一A介紹一種清洗液,用于除去拋光后基片表面的顆粒和金屬離子,溶液中含有羥基酸、含胺化合物、磷酸;W0200014785.A介紹的清洗液含有0.01%一5%四烷基季銨鹽氫氧化物。US2003077983.A1報道的酸基/堿性蝕刻劑或金屬蝕刻劑用于去除硬盤或磁頭表面吸附的拋光液顆粒等。
總的看來,現(xiàn)有的清洗劑主要以清洗某一特定的污染物為主,還缺少能高效去除對無機粒子、有機沾污以及金屬雜質(zhì)等的通用型清洗劑。目前報道和使用的這些清洗劑有一個共同特點,即含有強酸、強堿、強氧化劑(如羧基酸、鹽酸、氫氟酸、磷酸、氫氧化銨、四甲基氫氧化銨、雙氧水等)或有機溶劑,不僅有毒、污染環(huán)境,還具有很強的腐蝕性、易造成清洗后襯底損失過多和表面粗糙度變大等缺點[22矧。針對其不足,科研工作者正積極探索適合高精密表面清洗的低腐蝕性的新型清洗劑。
Y.L.Ku等人[24]在Si片CMP后清洗中發(fā)現(xiàn),擦洗時加入非離子表面活性劑可大大提高Si片CMP后清洗的效率及si片的可清洗性。T.M.Pan等人[矧在多晶硅CMP后清洗中添加螯合劑,有效提高了顆粒和金屬雜質(zhì)的去除效率,并研究了具有不同分子大小和電荷的螯合劑(EDTA、檸檬酸、草酸)的影響規(guī)律。
曹寶成等人嘶]研究了采用表面活性劑和螯合劑的新型超大規(guī)模集成電路清洗技術(shù)替代傳統(tǒng)的RCA清洗技術(shù),發(fā)現(xiàn)二者去污效果相當(dāng),但對Si片表面粗糙度的影響,前者更小。
作者已初步研究了不含強酸、強堿的不同種類表面活性劑(陰離子、非離子)組合使用對于硬盤清洗的影響,初步發(fā)現(xiàn)加入合適的表面活性劑,能防止粒子在表面的再沉積,對于SiO、/dO微粒均具有明顯的協(xié)同清洗效果。
可以看出,具有強腐蝕性為主的清洗劑已不適于高精度表面的清洗,高效、低腐蝕性、清洗對象廣的新型清洗劑將是清洗劑研究的發(fā)展方向。另外,不同作用的清洗劑可滿足不同清洗需要,分步清洗也是發(fā)展趨勢之一。
1.3清洗機理
清洗技術(shù)涉及到機械摩擦、流體力學(xué)、物理、化學(xué)、電化學(xué)等諸多學(xué)科知識。CMP后清洗機理研究一直是探討、提高CMP后清洗技術(shù)水平的重要途徑。擦洗的摩擦學(xué)機理得到了最廣泛研究。A.Phillipossian等人∞]分析了PvA刷擦洗的摩擦學(xué)特征及摩擦系數(shù)的影響因素。H.Liang等人【13J分析了擦洗處于邊界到彈流潤滑的摩擦學(xué)狀態(tài)。CMP后清洗過程中,粒子黏著機理及黏著力的大小對于顆粒的去除具有非常重要的作用【12J。Y.Liu等人[剮采用AFM測量了實際的CMP粒子與不同表面間的黏著力。R.Burtovyy等人[29]采用AFM測量了粒子/Cu表面的黏著力,認(rèn)為粒子/表面、粒子/粒子的相互作用力對清洗具有顯著影響。Y.K.Hong等人[30J研究了SiO對Cu表面的黏著力及化學(xué)添加劑對黏著和去除的影響,發(fā)現(xiàn)黏著力最低時,粒子去除率最高。G.Zhang等人LloJ假定粒子與表面的黏著力,T由范德華力和靜電力組成,給出擦洗過程中液力的拖曳力FD須大于/.zFT,粒子才能被移除(靜態(tài)摩擦系數(shù)廖為0.1—4),研究中對于粒子/表面存在的化學(xué)吸附作用未予以考慮。N.Dedy等人L3u采用微接觸模型,研究了納米顆粒在Si片表面的黏著與移去過程,認(rèn)為清洗中化學(xué)、機械作用結(jié)合對去除小粒子有效,對于大粒子則強的機械作用更有效。A.A.Busnaina等人【12J指出,拋光后Si片表面粒子的吸附會從起始的氫鍵逐漸轉(zhuǎn)化為強吸附力的化學(xué)吸附從而增加清洗的難度。劉玉嶺等人[32]分析了集成電路Si單晶襯底片表面顆粒污染的形成過程、si片表面吸附物吸附動力學(xué)過程以及吸附狀態(tài)控制機理,提出可以采用表面活性劑為物理吸附物質(zhì),有效降低顆粒污染。C.W.Uu等人[33]研究了Si片CMP后清洗中SiO粒子的靜電特性,提出提高pH值,可降低SiO粒子的Zeta電位,進而影響粒子的黏著、沉降性,從而改進清洗效果。
2CMP后清洗研究存在的問題及發(fā)展方向
目前,在集成電路芯片和計算機硬盤制造中,Si片和硬盤基片拋光后表面殘余污染物超標(biāo)是成品率下降的主要原因之一,高精表面的清洗問題已成為制約CMP技術(shù)水平提高的關(guān)鍵問題之一。為提高CMP后清洗技術(shù)水平,學(xué)者們已進行了很多有益的探索,但還存在以下不足:
①清洗機理方面。為簡化研究,現(xiàn)有黏著機理研究通常只考慮了粒子/表面間的物理吸附作用,對于粒子/表面間的化學(xué)吸附作用未予以充分考慮。而事實上,新拋光之后的磁盤新鮮表面由于失去表面上方的原子而存在高密度的不飽和鍵,以及在垂直表面方向上的位置弛豫效應(yīng)而形成的再構(gòu)表面和超結(jié)構(gòu),使其表面極不穩(wěn)定、活性極強,而拋光液中的納米磨粒由于粒子小并具有很高的活性,二者很容易形成化學(xué)鍵發(fā)生化學(xué)吸附。由于化學(xué)鍵強度遠(yuǎn)大于分子間作用力,導(dǎo)致納米粒子極難清洗。目前對于納米粒子的清除機理還了解甚少。拋光后新鮮表面存在的化學(xué)吸附作用不僅存在,并且還可能是主要的污染根源。因而不充分考慮粒子/表面間化學(xué)吸附作用的機理及相應(yīng)清洗技術(shù)的研究顯然是不夠的。
另外,現(xiàn)有清洗機理研究中,對于原子級精度表面的特殊性也未考慮。當(dāng)表面粗糙度達到原子級量級時,表面機械、化學(xué)、電化學(xué)行為都可能發(fā)生變化,這些都會影響污染物的吸附、脫附、表面的腐蝕等表面過程,從而影響清洗效率。在擦洗過程中,表面粗糙度還會影響清洗的摩擦學(xué)潤滑狀態(tài)等。機理的研究對開發(fā)高效、低投入的清洗設(shè)備和清洗劑,提高整個CMP技術(shù)的水平和加工質(zhì)量有著重要的促進作用。
②清洗劑方面?,F(xiàn)有清洗劑大多功能單一,并存在各種不足。如以與污染物反應(yīng)為清洗機理的強酸、強堿、氧化劑等,清洗的同時對表面也有很強的腐蝕性,不適合原子級表面的清洗;以降低界面張力、吸附為清洗機理的商品表面活性劑雖腐蝕性很小,但結(jié)構(gòu)簡單、單獨使用對納米粒子的清洗能力還不夠理想。納米粒子的清洗是目前CMP后清洗的主要難點之一。因而需要根據(jù)工件表面物化特點以及納米粒子的特性等,針對性地研制高效的新型表面活性劑。
3結(jié)語
CMP拋光后表面的清洗質(zhì)量直接關(guān)系到CMP技術(shù)水平的高低。迄今,國外對先進電子產(chǎn)品制造中的超精密加工技術(shù)嚴(yán)格保密。高水平CMP的后清洗中的關(guān)鍵技術(shù)包括清洗設(shè)備、清洗工藝、清洗劑等全部依賴進口,嚴(yán)重制約了我國超精密加工技術(shù)的發(fā)展。因此面對日益提高的器件表面質(zhì)量的要求,急需探索與開發(fā)針對原子級平整表面的“超凈、無損傷”清洗技術(shù)。努力開展相關(guān)的清洗機理、清洗設(shè)備、清洗劑以及新型清洗技術(shù)等方面的研究具有重要的理論與實際意義。(免責(zé)聲明:文章來源于網(wǎng)絡(luò),如有侵權(quán)請聯(lián)系作者刪除。)