氮(氧)化硅濕法刻蝕后清洗方式的改進
摘要:在半導體制造工藝的濕法刻蝕中,用熱磷酸刻蝕氮化硅和氮氧化硅是其中一個相對復雜又難以
控制的工藝。在這個工藝中,熱磷酸刻蝕后的去離子水(DIW)清洗更是一個非常重要的步驟。主要分
析了由于去離子水清洗不當造成的表面缺陷的形成機理,并通過合理的實驗設計和分析,給出了具體的解
決方案。
關鍵詞:半導體制造;氮化硅;濕法刻蝕;濕法清洗;
1引言
熱磷酸濕法刻蝕已經(jīng)在半導體制造工藝中應用了幾十年了。由于熱磷酸對氮化硅和氮氧化硅刻蝕具有良好的均勻性和較高的選擇比,一直到了90nm的最先進制程也是采用熱磷酸來刻蝕氮化硅與氮氧化硅。常用的熱磷酸刻蝕液是由85%濃磷酸和15%去離子水(DIW)配合而成,并保持在160℃的溫度下進行刻蝕。熱磷酸刻蝕之后的芯片一般采用熱去離子水清洗。當芯片從160℃的磷酸槽進入水槽時,芯片表面殘余磷酸的粘度極劇增加,并且形成一層帶有磷酸和副產(chǎn)物的薄層緊貼于芯片表面。如果不將這層殘余物質(zhì)清洗干凈,將嚴重影響芯片的后續(xù)制程,造成芯片成品率的損失和可靠性問題。所以熱磷酸后清洗比其他酸液(如SC2,SPM,HF等易去除的試劑)之后的清洗更關鍵,也更具有挑戰(zhàn)性[1]。
2清洗缺陷產(chǎn)生機理分析隨著工藝尺寸的逐漸縮小,定義和刻蝕精準的多晶硅線條變得越來越困難。工業(yè)界常采用在多晶硅表面覆蓋一層由化學汽相沉積的氮氧化硅(SiON)來解決這個問題。在定義多晶硅線條的光刻膠時,氮氧化硅可作為防反射層(ARC),使光刻更精確;而在多晶硅刻蝕時,氮氧化硅可以當作硬掩膜,即先將氮氧化硅刻蝕出線條形狀,然后以氮氧化硅線條為掩膜來刻蝕下面的多晶硅,這樣可以避免由于光刻膠邊緣受離子轟擊變薄而使多晶硅線條受損。
在多晶硅刻蝕結(jié)束后,需要將這層已經(jīng)沒有用的氮氧化硅去除,否則會影響之后的金屬硅化物的形成。工業(yè)界一般采用熱磷酸濕法刻蝕法去除這層氮氧化硅。這是由于這種刻蝕對氮氧化硅/多晶硅的選擇比很高,反應不會影響多晶硅線條的尺寸,對源漏區(qū)剩余氧化硅的刻蝕也很少。氮氧化硅濕法刻蝕流程如圖1所示。
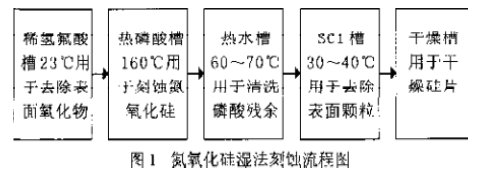
但是由于在氮氧化硅濕法刻蝕時表面的特殊性質(zhì),很容易在此工藝中產(chǎn)生表面缺陷,以致影響芯片的良率與可靠性。在多晶硅刻蝕之后,芯片表面存在兩種不同的物質(zhì):一個是占面積絕大部分的氧化硅(主要是用作淺溝道隔離的氧化硅),是親水性的物質(zhì);另一個是多晶硅線條,多晶硅是憎水性的。芯片表面同時存在親水性和憎水性的物質(zhì)時,就特別容易在去離子水中吸附其中的空氣氣泡[2]。
水槽中空氣氣泡的成因很多。首先是水槽的熱水管較易積累氣泡。熱水管不是常開的,只有在水槽內(nèi)有芯片時才會開啟,平時處于關閉狀態(tài)時,管路內(nèi)的氣泡會累積在閥門下方的管壁上。一旦閥門開啟就進入水槽,從而影響水槽中的芯片;又由于整個熱水管路是一個密閉系統(tǒng),水中空氣會因加熱而析出。另外由于水槽中的熱水是由酸槽附屬的去離子水加熱器提供,當加熱器加熱時,緊貼加熱部位的去離子水會產(chǎn)生局部沸騰現(xiàn)象,也會產(chǎn)生氣泡??傊?,如果熱水并不是由廠務集中供應,而是使用機臺自帶的加熱器時,熱水槽的氣泡是不可避免的。
這些氣泡會隨水流由水槽底部進入水槽,部分氣泡會吸附在靠近液面處的芯片表面,阻礙熱水對剩余磷酸的清洗。而多晶硅刻蝕完后芯片表面凹凸不平的“地貌”,使得芯片從熱磷酸中取出時,表面殘留更多的磷酸溶液。磷酸會繼續(xù)與底下的氧化硅反應產(chǎn)生副產(chǎn)物,副產(chǎn)物會在之后的清洗中剝落,隨著水流遷移到芯片各處(圖2)。副產(chǎn)物會嚴重增加芯片的表面缺陷數(shù)量,如果副產(chǎn)物落在多晶硅線條邊晶體管源漏的位置,不僅會影響漏源的離子注入,還會影響晶體管邊墻的形狀,嚴重地會造成鎢接觸開路(圖3)。
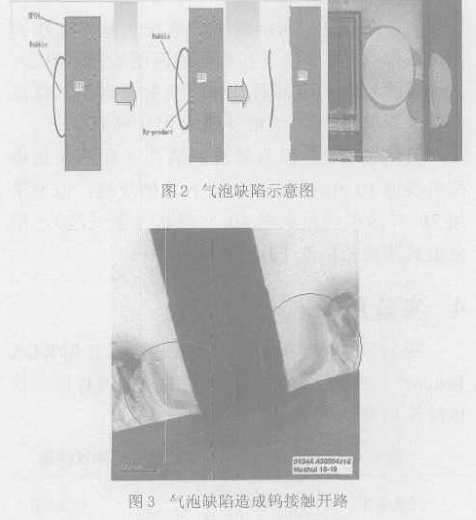
3實驗方法
基于上述對熱磷酸后清洗表面缺陷產(chǎn)生機理的分析,本文擬利用圖形化200mm硅片,采用標準的和不同改進的熱磷酸后清洗方法,以確定清洗效果最佳的后清洗方案。
實驗采用的是美國SCPGlobal公司生產(chǎn)的適用于200mm硅片的濕法清洗機(型號E200)。配置有熱磷酸槽(160℃)、水槽和使用異丙醇(IPA)的干燥槽。水槽內(nèi)配有去離子水加熱器,可輸出70℃去離子水。
實驗硅片為剛經(jīng)過多晶硅刻蝕的正常圖形化200mm硅片,并且用KLATencor?2360缺陷測試儀測量清洗前后硅片表面的缺陷數(shù)量,以便對比分析不同清洗方法的清洗效果。
清洗條件1:普通熱水溢出式清洗。硅片在熱磷酸中浸泡10min,立即進入水槽,通70℃熱水,不斷繼續(xù)溢出式清洗,清洗10min后進入干燥槽。
清洗條件2:熱水快速排水式清洗。硅片在熱磷酸中浸泡10min,立即進入水槽,通70℃熱水,先進行2min的溢出式清洗,后采用排水式清洗(即用幾秒鐘將水槽排空,在關上閥門補水,補滿水后再將水槽排空,以此循環(huán))。共10min,最后經(jīng)干燥槽干燥。
清洗條件3:水淋排水式清洗?;玖鞒掏逑礂l件2,不同的是在水槽的兩側(cè)安裝水淋器,在水槽排空時將水淋器打開,噴射去離子水以覆蓋整個芯片表面,水槽補滿時停止噴水。
清洗條件4:溫水溢出式清洗。硅片在熱磷酸中浸泡10min后,立即進入水槽浸泡,但不采用70℃熱水,而采用40℃溫水(無氣泡),用溢出式清洗法清洗10min后干燥。
4實驗結(jié)果與討論
四個不同清洗條件的硅片實驗之后在用KLATencor?(2360)機臺測量其表面缺陷的數(shù)目。具體結(jié)果如表1所示。酸殘余,也沒有發(fā)現(xiàn)水痕,清洗效果最好,遠優(yōu)于其他清洗方式;而采用溫水溢出式清洗(清洗條件4)的芯片表面存在著無規(guī)則分布的小粒磷酸殘余,這類殘余并不是氣泡產(chǎn)生而是因為溫水洗凈率不夠,所以殘余的大小往往不足0.5μm,而且大多分布在空曠區(qū)。這類小的殘余可以在接下來的清洗中用熱的硫酸等非常容易地去除。
經(jīng)過多次試驗都證明:淋排水式清洗(條件3)是最佳的清洗方式,并轉(zhuǎn)入實際生產(chǎn)應用。經(jīng)過此清洗方式的改變,中芯國際一廠某典型產(chǎn)品(0.18μm工藝)芯片邊緣新月狀失效的發(fā)生率由12%下降到0,平均成品率由65%上升至80%。
5結(jié)論
在分析對氮(氧)化硅熱磷酸刻蝕后清洗的表面缺陷產(chǎn)生機理后,通過一系列的后清洗實驗設計和分析,結(jié)果表明:考慮到磷酸殘余在低溫時的高粘稠性,必須用較高溫度的去離子水清洗,同時,為了防止熱水中特有氣泡缺陷,推薦在水槽兩側(cè)安裝水淋器以保證芯片一直處于水的氛圍中。另外,由于清洗時間不足或是水溫不夠造成的磷酸殘余可以用其他的高溫溶劑清洗。建議在氮氧化硅刻蝕之后加一步熱硫酸清洗,不僅可以防止磷酸殘余,更可以去除由于刻蝕造成的有機物污染。(免責聲明:文章來源于網(wǎng)絡,如有侵權請聯(lián)系作者刪除。)