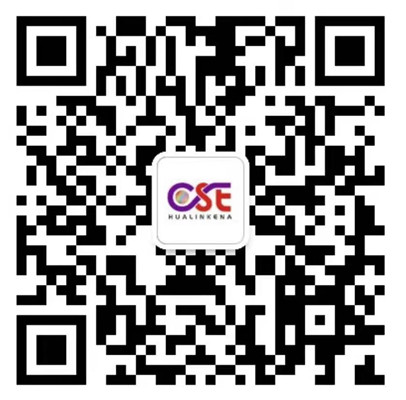
掃碼添加微信,獲取更多半導體相關資料
引言
概要掃描探針顯微系統( SPM )、電子背散射板( ebsd )、極化曲線測量晶體組織對硫酸-過氧化氫蝕刻引起的銅蝕刻速率的影響 接近{001}面的方位快,被蝕刻發(fā)現被凹陷后,{111}和{101}面附近的方位被緩慢蝕刻。 顯示出大蝕刻速率的多晶體銅,腐蝕電位高,局部陰極反應的極化小。 這表明,多晶體銅的蝕刻速率由各個晶面的過氧化氫還原反應速度的平均值決定。為了調查多晶體的蝕刻速率與晶體組織的關系,測量了軋制銅材、添加劑和成膜條件下晶體組織發(fā)生變化的電解鍍銅膜的蝕刻速率。 制作的試料的結晶組織用EBSD進行了分析。 進而,通過極化曲線的測量,考察了晶體組織的不同對蝕刻反應的影響。另外,作為緩和組織不同引起的蝕刻速率差、降低咬邊的方法,報告了向蝕刻液中添加1 -丙醇的影響。
?
實驗
以無氧銅板三菱伸銅制C1020為試料,作為預處理,以85%磷酸中的試料為陽極,通過極間電壓為2 V的恒壓電解進行電解研磨,在去除加工變質層的同時使表面平滑。 之后,利用TSI公司制造的帶有EBSD系統的FE-SEM日本電子制造的JSM-7001FA,對各個晶粒的方位進行了鑒定。 該試料用SII納米技術制造的SPM Nano Cute,測量與EBSD測量同視野的SPM像,得到了試料表面的三維形狀像。 測量視野為50 m 50 m。 然后,用轉速設定為500 rpm的磁力攪拌器攪拌保持在25℃的1 mol/dm3過氧化氫、0.72 mol/dm3硫酸混合水溶液,將試樣浸漬在其中15 s,水洗、干燥后,測量同視野的SPM像,進行蝕刻。表?1表示試樣制作條件。
蝕刻速率的測定
實驗裝置的概略如圖1所示。 在設置于恒溫槽內的反應容器內充滿0.72 mol/dm3硫酸、1 ?mol/dm3過氧化氫混合水溶液,反應容器內的溫度達到了規(guī)定溫度。之后,將試樣浸漬在容器內,開始溶解。 溫度定為25攝氏度。
?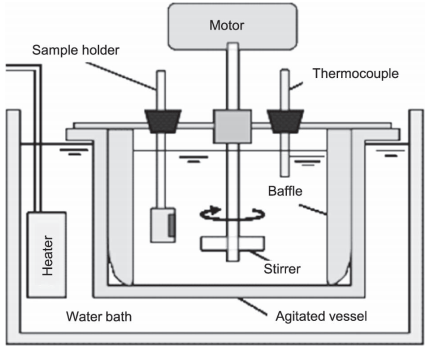
圖1
使用圖2所示的電解單元,利用墊片使試料和電解液的接觸面積一定。 對電極使用的是Pt板電極,參比電極使用的是外筒液使用飽和硝酸鉀水溶液的雙結結構的飽和Ag/AgCl電極( +199 mV vs. SHE )。 電解液使用的是0.72 mol/dm3硫酸、1 mol/dm3過氧化氫混合水溶液和0.72 mol/dm3硫酸水溶液。 浴溫設定為25℃,用轉速設定為500 rpm的攪拌器攪拌電解液。 電位掃描速度為設定為1 mV/s,從自然電位向陰極方向進行了掃描。 之后,更換試料,從自然電位向陽極方向進行掃描,制成極化曲線。
?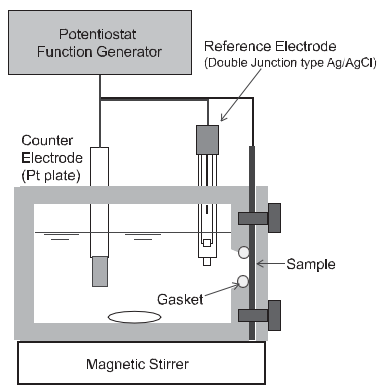
圖2
圖3(a )、( b )顯示的是利用SPM測量的15秒蝕刻前后的試料表面三維形狀像。 蝕刻前的試樣是只有幾納米級凹凸的非常平滑的形狀。 用EBSD測量的與?圖 3(b )視野相同的IPF (逆極性圖像)圖如圖 3(c )所示。 圖 3(b )、( c )中記載了根據EBSD鑒定的各晶粒的密勒指數。 在蝕刻后的圖3(b )中,由于結晶方位不同,蝕刻速率不同,因此形成的凹凸得到了明確確認。沒有觀察到晶界的優(yōu)先溶解。
圖 4顯示的是在標準立體三角形上繪制蝕刻迅速進行、凹陷的面和蝕刻緩慢凸出的面的結果。 其中顯示,接近{001}面的方位被快速蝕刻,接近{111}和{101}面的方位被慢蝕刻。 由于{001}面溶解最快,因此可以預想優(yōu)先取向于{001}面的銅的蝕刻速率會變大。通過添加1 -丙醇,可以緩和晶體組織不同引起的蝕刻速率差,半加成工藝軟蝕刻時產生的咬邊有望降低。
?
討論和結果
研究表明,硫酸-過氧化氫蝕刻液中銅的蝕刻速率依賴于晶體取向,{001}面的蝕刻速率最大。 通過極化曲線測量發(fā)現,銅的結晶方位一方面不影響銅的溶解反應,另一方面對過氧化氫的還原反應有很強的影響。 因此,認為蝕刻速率隨晶體組織而變化的原因是,過氧化氫的還原反應活性因晶體取向而異。