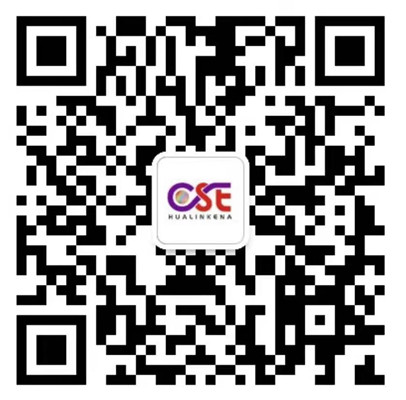
掃碼添加微信,獲取更多半導體相關(guān)資料
引言
本文在高真空組合工具中研究了氣相預柵極氧化物表面制備:用無水氟化氫蒸汽和甲醇蒸汽蝕刻二氧化硅并通過改變晶片溫度、室壓和氣體流速,這樣就可以很好地控制氧化物蝕刻速率。本實驗已經(jīng)實現(xiàn)了氧化物蝕刻速率的5%的標準誤差。在60/分鐘的氧化物蝕刻速率下,每125毫米晶片產(chǎn)生的顆粒少于10個。原子力顯微鏡測量顯示沒有增加硅表面的微觀粗糙度,這歸因于蒸氣氟化氫(HF)蝕刻。
?
介紹
現(xiàn)代集成電路(IC)制造中最重要的工藝之一是預柵氧化晶片表面制備。事實表明,金屬氧化物半導體(MOS)器件的性能取決于柵極氧化物生長之前的清潔工藝。然而,在傳統(tǒng)制造工藝中,每次工藝完成后,晶圓會在潔凈室中從一個工具轉(zhuǎn)移到另一個工具,因此會面臨再次污染的風險。對于一些關(guān)鍵的工藝順序,例如柵極氧化物生長,應該在晶片清洗后立即生長氧化物,以減少氧化物缺陷并獲得高的器件成品率。
為了實現(xiàn)無污染制造,集群是選項之一。組合工具允許單晶片處理,在此期間,晶片在真空下在處理模塊之間轉(zhuǎn)移,并且降低了再污染的風險。配備原位診斷,可以更好地控制過程穩(wěn)定性。隨著晶片尺寸越來越大,單晶片加工變得越來越有吸引力。與真空兼容的氣相清潔工藝目前正受到越來越多的關(guān)注。在氣相過程中,氧化物和其他表面污染物可能會通過活性氣體和表面層/污染物之間的反應而被去除。氣相處理也具有清潔較小特征的潛力,因為濕法處理受到溶液表面張力的限制。氣相處理的另一個優(yōu)點是與濕法分批處理相比減少了化學品消耗。因此,氣相處理是環(huán)境友好的。
例如,表1總結(jié)了從我們的研究機構(gòu)收集的數(shù)據(jù)。數(shù)據(jù)顯示了一個月周期的預柵極氧化物清洗過程的平均值。可以看出,除了HF以外,直接比較是困難的,因為兩個方案中使用的化學物質(zhì)基本上是不同的。然而,我們已經(jīng)觀察到在氣相清洗中消耗的HF的量比在氣相清洗中少大約六分之一濕法清洗,與濕法清洗相比,在濕法批處理過程中消耗了大量的去離子水,以及在氣相清洗中消耗的化學物質(zhì)的量很少。
除了氣相處理本身的有效性之外,氣相處理的成功取決于單晶片處理技術(shù)的大規(guī)模實施。我們在這篇文章和其他6–11中得出結(jié)論,氣相處理對于預柵氧化清洗是有前途的。潔凈室中微環(huán)境概念的采用將導致制造中更多的單晶片加工工具。這一點,再加上對危險化學品消耗和處理的更嚴格的規(guī)定,將加速該技術(shù)的實施。
在這篇文章中,我們報道了我們在高真空集成系統(tǒng)中對二氧化硅的氟化氫蒸氣腐蝕和紫外輔助清洗的研究。我們提供了關(guān)于氧化物蝕刻、表面微觀粗糙度、清洗過程中的顆粒生成和金屬污染物去除的數(shù)據(jù)。我們還研究了柵氧化層的電學性質(zhì)以及氣相清洗和快速熱氧化形成的SiO2/Si界面。這些結(jié)果已在最近發(fā)表的一篇文章中作了總結(jié)。
?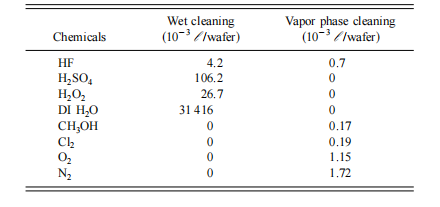
表1 傳統(tǒng)濕法/批量清洗和汽相/單晶片清洗的化學消耗比較
通過讓N2鼓泡進入室內(nèi)。通過改變N2流速來調(diào)節(jié)甲醇的量。所有引入室內(nèi)的氣體都是半導體級的,并經(jīng)過過濾以確保超高的純度和清潔度。
?
結(jié)果和討論
二氧化硅蝕刻
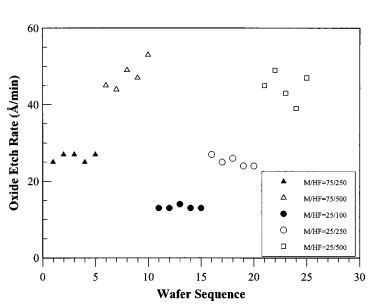
圖4?
?
為了找到工具給出最佳氧化物蝕刻性能的工藝窗口,進行了實驗設(shè)計。實驗的一個結(jié)果顯示在圖5中,其中氧化物蝕刻速率標準誤差被繪制為氧化物蝕刻速率的函數(shù)。圖中的每個數(shù)據(jù)點代表一個處理五個晶片的配方。蝕刻速率的變化隨著蝕刻速率的增加而增加。存在一個可以實現(xiàn)小于5%的變化的工藝窗口??梢钥闯?,其中三個配方已經(jīng)重復和確認。通過仔細設(shè)計工藝,可以實現(xiàn)更小的變化。為了控制晶片之間的可重復性,蝕刻速率最好小于100/min。
?
表面形態(tài)
Si/SiO2界面粗糙度通常導致更高的漏電流或SiO2介電膜的早期介電擊穿。14,15 Si表面微觀粗糙度可以增加在HF蝕刻、化學清洗甚至去離子水沖洗過程中。15–18原子級光滑表面是形成柵極氧化物的理想選擇。
如上所述,氧化物蝕刻速率在氣相HF氧化物蝕刻工藝中波動。需要過蝕刻來保證完全去除犧牲氧化物。由于過度蝕刻造成的表面粗糙是不理想的。圖6(a)是被蒸氣HF侵蝕的Si(100)表面的AFM圖像。蝕刻在50℃和200托的室壓下進行3分鐘,相當于60/分鐘的氧化物蝕刻速率。該表面的均方根(rms)粗糙度為0.24納米。作為比較,用100∶1的HF水溶液蝕刻Si(100)表面2分鐘的結(jié)果顯示在圖6(b)中。這里,均方根值為
0.26納米。因此,在蒸汽和含水HF腐蝕的Si(100)表面之間沒有觀察到差別。

圖5 氧化物蝕刻速率標準誤差是氧化物蝕刻速率的
二氧化硅蝕刻過程中的顆粒生成
在濕法清洗和去離子水沖洗過程中,顆??赡軙≡谝后w頂部。當將晶片從溶液中拉出時,它們中的一些可能會重新沉積在晶片表面上。汽相處理的優(yōu)點之一是不需要去離子水沖洗。
?
總結(jié)和結(jié)論
我們已經(jīng)研究了氣相處理在高真空組合工具中用于預柵極氧化物清洗應用的能力。對于50℃的溫度和200托的處理窗口的室壓,氧化物蝕刻是可再現(xiàn)的,晶片與晶片之間的標準誤差小于5%。沒有觀察到增加的硅表面微觀粗糙度,即使在侵蝕性的蒸汽HF蝕刻之后。在蝕刻速率為60/分鐘的情況下,蝕刻過程中每個晶片大約產(chǎn)生8個顆粒。較高的氧化物蝕刻速率通常會導致較大的顆粒沉積。已經(jīng)通過清洗程序證明了金屬污染物的去除,包括蒸汽HF蝕刻,隨后是UV/Cl2曝光。氣相清洗技術(shù)是未來組合工具、單晶片加工發(fā)展的重要選擇。