?
?LED?芯片是一種將直接電能轉化為光能的半導體器件,是現(xiàn)代信息產業(yè)的核心器件。隨著我國科學技術的不斷進步與微電子設備研制的發(fā)展,國內從事芯片設計制造企業(yè)也逐漸增長到幾百家,但是他們普遍自主知識產權及自主創(chuàng)新設計制造水平不高。LED?芯片制造及高端
??封裝技術是技術密集型產業(yè),其發(fā)展水平離不開高端工藝與硬件設備。近年來國內微電子設備產業(yè)急速擴張,而支撐其技術引領的高端設備卻嚴重缺乏,發(fā)展瓶頸逐漸成形。目前產業(yè)高端設備依然依賴國外進口,亟需開發(fā)研制自己的高端設備。
LED?封裝就是在保證其芯片無損以及高光取出效率的前提下將外部引線與內部芯片電極相互連接。在整個LED?產業(yè)鏈當中,封裝技術是產業(yè)與市場的連接紐帶,而在?LED?芯片制造和高端封裝過程當中去膠這一工藝過程起著非常重要的作用。
1?當前面向?LED?芯片制造和封裝去膠設備現(xiàn)狀
??隨著科學技術水平的不斷發(fā)展,集成電路技術現(xiàn)已主要通過凸點封裝模式來大幅提升封裝密度與效率。凸點封裝技術包括了膜沉積、光照、去膠等多項半導體芯片制備技術。現(xiàn)代高端封裝工藝一般面向?300 mm?晶圓、65 nm?及以下極大規(guī)模集成電路封裝需求,開發(fā)凸點個數(shù)3000?以上、間距?200?μm?以內的小間距凸點制作技術和再布線技術。其核心過程是在已制成芯片的特征位置定義并形成凸點、重布層(RDL)或通孔(Via)等特征圖形。由于特征尺寸的縮小、特征圖形密度的增加,其特征圖形的定義就必須通過涂覆超厚膠 膜 、光刻、顯影、去膠等工藝制程來實現(xiàn)。
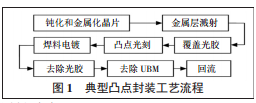
? ? 圖 1 為典型凸點封裝工藝流程圖,其中光刻膠膜較厚,通常會達到?50~100?μm。由于電鍍產生的凸點一般會有類似蘑菇頭的結構,當凸點密度較大時,采用傳統(tǒng)槽式去膠,其根部的光刻膠不易去除干凈,會影響后續(xù)的UBM?刻蝕,造成回流后凸點高度的不一致。因此急需開發(fā)一種高密度凸點封裝工藝中所必須的全自動去膠機。
??目前半導體?IC?封裝的主要發(fā)展趨勢為多引腳、窄間距、小型、薄型、高能、多功能、高可靠性和低成本,對系統(tǒng)集成的要求越來越迫切,三維集成封裝技術由此應運而生。三維集成封裝的兩種最通用技術是通過傳統(tǒng)打線結合結構的使用,以及通過穿硅通孔(TSV)技術建立芯片疊層的元件之間的電子連接性。然而,當?I/O?個數(shù)和疊層數(shù)量增加的時候,打線接合已經不實用。利用TSV?技術實現(xiàn)芯片間的垂直通孔,從而達到最大的堆疊密度和最小空間尺寸。TSV?技術已經在邏輯線路、存儲器、CMOS?圖像傳感器(CIS)等產品的封裝技術中得到部分應用,TSV在三維集成封裝制造過程中已經變得越來越迫切。
??相對于傳統(tǒng)凸點封裝,3D-TSV?工藝對新型光刻膠噴涂機、圓片鍵合機、硅片減薄機、TSV?等離子刻蝕機和雙面光刻機提出了新的需求。目前國內?LED?芯片和封裝生產企業(yè)所采用的去膠設備均為手動或半自動去膠槽,化學液消耗量較大,工藝參數(shù)不易控制,結果重復性差。
??在高端封裝和?LED?工藝中,光刻膠膜一般較厚,通過開發(fā)面向?LED?芯片制造和高端封裝旋轉式去膠機,實現(xiàn)高壓噴射去膠液或常壓噴灑去膠液,結合兆聲波的方法快速干凈地去除光刻厚膠。因此研制滿足?LED?芯片制造和高端封裝(如:BGA、MCM、WLP、3D-TSV?等)生產需要的全自動濕法去膠設備(簡稱去膠機)尤為重要。同時,該設備與雙面光刻機、通孔(TSV)刻蝕機、圓片減薄機、高密度倒裝機、電鍍機、硅片清洗機等聯(lián)線,組成高密度封裝和LED成套工藝設備,可以促進當前高端封裝技術發(fā)展。
2?旋轉式去膠機的設計
2.1?布局設計
??通過對滿足?LED?芯片制造和高端封裝生產需要的自動濕法去膠設備的研制,實現(xiàn)該設備與雙面光刻機、通孔(TSV)刻蝕機、圓片減薄機、高密度倒裝機、電鍍機、硅片清洗機等聯(lián)線,組成 高 密 度 封 裝 和LED成套工藝設備。整個 設 備 的 布局如圖?2?所示,主要有電控單元、化學液供應單元和反應腔體單元,其技術開發(fā)的核心是反應腔體的設計。
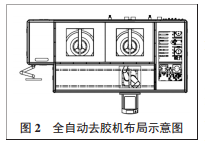
2.2?反應腔體單元結構設計
??全自動旋轉去膠機的反應腔體主要由三大部分組成:擺臂系統(tǒng)、夾持系統(tǒng)和回收腔。其中,擺臂系統(tǒng)主要完成反應腔體化學液體、氮氣以及水的傳送,在該系統(tǒng)中所有反應物質通過該系統(tǒng)實現(xiàn)在清洗目標硅片上的均勻分布,提高去膠效果;夾持系統(tǒng)主要完成去膠硅片的夾持工作,在夾持硅片的過程中利用氣壓傳動技術實現(xiàn)其高速旋轉,同時保證硅片正面清潔無污染,為提高去膠效果,該系統(tǒng)還可以同時完成直線上下和旋轉運動;回收腔主要完成化學液和水的回收,為提高化學液的利用效率實現(xiàn)循環(huán)利用,回收腔采用分層設計,不同的化學液體將在回收腔中實現(xiàn)分類回收。
??該反應腔體結構示意圖如圖?3?所示。該反應腔體在搖擺送液手臂以及其他裝置的作用下,可以完成不同種類化學去膠以及水洗清潔干燥等自動化同時進行,實現(xiàn)良好的去膠效果。該裝置工作時,首先會將通過夾持裝置將目標硅片鎖定在腔體的底層,通過擺臂系統(tǒng)均勻將一種化學液噴灑在硅片上,并完成去膠和回收;再通過夾持裝置將硅片提升至圖?3?所示位置,擺臂系統(tǒng)再次輸送其他化學液,完成去膠和廢液回收;最后直至光刻膠去除完全后,硅片在夾持系統(tǒng)作用下升至頂部,完成水洗、干燥和廢液回收,完成整個去膠工序。
2.3?主要技術指標及效益
通過對面向?LED?芯片制造和高端封裝旋轉式去膠機的設計與研究,設備達到如下指標:1)晶片尺寸:準200~300 mm;
2)去膠腔體:2~4?個;
3)去膠方式:全自動單片旋轉濕法噴淋式、化學液高壓噴射和兆聲波;
4)去除膠層:5 ~50?μm?正膠、50 ~120?μm?負膠;
5)去?膠?化?學?液?:含DMSO、NMP?等各種去膠液;
6)去膠液溫度:25~80?℃,1?℃;
7)去膠速率:10~20μm/min以上;
8)顆粒去除:0.5μm顆粒?95%以上。
??市場需求不斷提高,生產工藝技術不斷改進等外、內部因素無不促使面向?LED?芯片制造和高端封去膠設備需不斷進步,這樣才能在涉及半導體、光通信、PCB?等領域充分滿足不同客戶的需求。
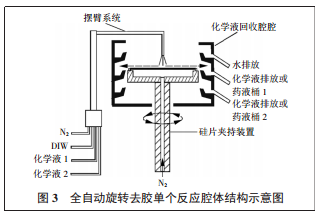
3?結 論
??面向?LED?芯片制造和高端封裝旋轉式去膠機的設計與研究可以對當前封裝領域去膠設備有效補充,同時該設備研究可以實現(xiàn)快速去除厚度在?50~120?μm?的厚感光膠膜;清洗?Bump?根部和3D-TSV?深孔底部的光刻膠殘留;單片去膠時,硅片正面噴灑化學液,有效地保護硅片的背面不被化學液污染;有效設計反應膠,通過進風與排風的有效配合,使整個腔體內部流動的氣體形成層流,從而帶走去膠過程所形成的水氣和濺射出的光刻膠,避免硅片表面的二次污染;新型化學液供應系統(tǒng),在化學液噴灑過程中保持穩(wěn)定的工作溫度,尤其是在某些制程需要高溫化學液(如?70?℃);能夠回收噴灑后的化學液,在線去除化學液中的光刻膠殘留,循環(huán)使用化學液,節(jié)約成本等顯著特點,具有十分重要的現(xiàn)實應用價值。
更多的半導體材料工藝設備相關資訊可以關注華林科納CSE網站:
126xa.cn,現(xiàn)在熱線咨詢400-8768-096,可立即獲得免費的半導體清洗解決方案。
?